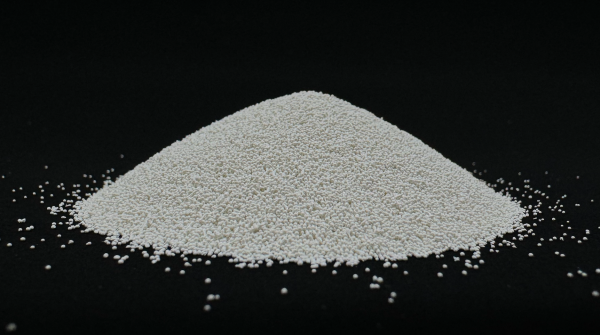
(ceramic sand)
Shanghai, China, 17th Dec 2024 – In today’s fast-paced manufacturing landscape, achieving precision, efficiency, and sustainability is a growing challenge. Surface treatment, a critical step in many industries, often determines the quality and durability of a final product. Among the tools driving advancements in this field, ceramic blasting media is emerging as a transformative solution. Known for its exceptional performance and environmental benefits, ceramic blasting media is setting a new standard for modern surface treatment techniques.
The Role of Surface Treatment in Manufacturing
Surface treatment encompasses processes like cleaning, smoothing, deburring, and preparing surfaces for coating or bonding. These steps are essential in industries like aerospace, automotive, and consumer electronics, where precision and quality are paramount.
Traditional surface treatment methods often rely on abrasives such as steel shot, glass beads, or garnet. While effective, these materials can pose challenges such as inconsistent results, excessive wear on machinery, and environmental concerns due to their short lifecycle and waste generation. These limitations underscore the need for a more advanced solution—one that ceramic blasting media fulfills.
Why Ceramic Blasting Media Stands Out
Ceramic blasting media distinguishes itself with its unique material properties and unmatched performance benefits:
- Exceptional Material Properties:
- Hardness and Durability: With a consistent hardness level, hlh ceramic media withstands repeated use without breaking down, ensuring consistent performance over time.
- Uniformity: Its spherical shape ensures even and precise surface treatment, reducing the risk of over-blasting or uneven finishes.
- Low Dust Generation: Unlike traditional abrasives, ceramic media produces minimal dust, creating a cleaner and safer work environment.
2、Superior Performance Benefits:
- Precision for Complex Parts: Ceramic media excels in treating intricate components without damaging their integrity, making it ideal for delicate industries like electronics and aerospace.
- Cost Savings: Its longevity reduces consumption rates and minimizes downtime for media replacement.
- Enhanced Surface Finish: It creates smooth, uniform surfaces, improving the adhesion of coatings and paints.
3、Comparison with Alternatives:
- Steel Shot: While durable, steel shot can be too aggressive for delicate surfaces.
- Glass Beads: These are prone to breakage and dust generation, making them less cost-effective.
- Garnet: A natural abrasive with limited reusability compared to ceramic media.
Applications in Modern Manufacturing
Ceramic blasting media is transforming surface treatment across industries, addressing challenges that traditional methods cannot overcome.
- Aerospace:
The aerospace industry relies on ceramic media for deburring lightweight alloys, cleaning turbine components, and preparing surfaces for coatings. Its precision ensures that critical parts meet stringent safety and performance standards. - Automotive:
Ceramic media enhances the surface integrity of engine components, gears, and other critical parts, contributing to improved performance and longevity. - Consumer Electronics:
In the electronics industry, ceramic media plays a key role in polishing delicate components, such as smartphone casings and microprocessors, ensuring flawless finishes that meet consumer expectations. - Emerging Applications:
With the rise of additive manufacturing and 3D printing, ceramic media is becoming indispensable for post-processing, providing smooth finishes and removing support structures efficiently.
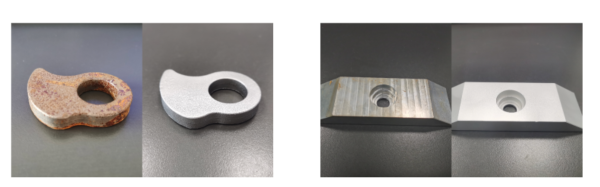
(Comparison of workpieces treated with ceramic sand before and after)
Sustainability and Cost Efficiency
Sustainability is a growing priority in manufacturing, and ceramic blasting media offers a compelling solution:
- Reduced Waste: Its recyclability allows for multiple cycles of use, minimizing waste generation.
- Environmental Safety: Low dust production reduces environmental contamination and improves workplace safety.
- Cost-Effectiveness: Though initially more expensive than some traditional abrasives, ceramic media’s longer service life and efficiency result in lower total costs over time.
A case study illustrates this advantage: A major automotive manufacturer reported a 30% reduction in media consumption and a 20% increase in productivity after switching to ceramic blasting media.
Choosing the right supplier is crucial to maximizing the benefits of ceramic blasting media. Our company specializes in providing high-quality solutions tailored to diverse industry needs.
- Ceramic Blasting Media: The pinnacle of surface treatment materials, delivering unmatched performance and sustainability.
- Aluminum Oxide: A versatile abrasive for aggressive cleaning and surface preparation.
- Zirconia Beads: Known for their durability, ideal for demanding applications.
- Plastic Media: A gentle yet effective solution for delicate surfaces and aerospace applications.
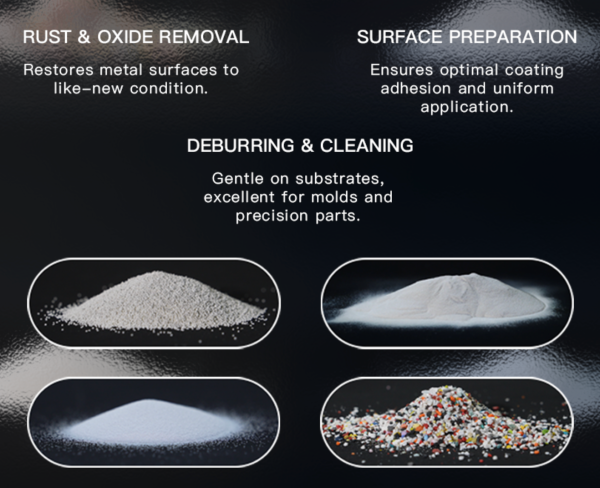
Our products have earned the trust of manufacturers worldwide, with proven results in enhancing productivity, reducing costs, and meeting the highest industry standards.
Ceramic blasting media is more than just an abrasive—it’s a catalyst for efficiency, precision, and sustainability in surface treatment. As industries face growing demands for quality and environmental responsibility, adopting advanced materials like ceramic blasting media is no longer an option but a necessity.
Contact us today or visit www.hlh-js.com to explore how our advanced solutions can meet your needs.
Media Contact
Organization: Jiangsu Henglihong Technology Co., Ltd
Contact Person: Zoey Fang
Website: https://hlh-js.com/
Email: Send Email
City: Shanghai
Country: China
Release Id: 17122421525
The post Revolutionizing Surface Treatment: The Impact of Ceramic Blasting Media on Modern Manufacturing appeared on King Newswire. It is provided by a third-party content provider. King Newswire makes no warranties or representations in connection with it.
Disclaimer: The views, suggestions, and opinions expressed here are the sole responsibility of the experts. No Insta Daily News journalist was involved in the writing and production of this article.